A Fire Door Survey is Just Checking a Fire Door, Right?
Well, in short no!
The news and social media platforms are awash with stories of the inadequate state of fire doors – continually providing imagery of the poor fire door conditions throughout the UK. Due to the frequency and easy accessibility of these images, this is no longer shocking, it’s as regular as putting milk on your cornflakes.
Companies who inspect, remediate and replace fire doors could look at this with dismay, and consider the mountain the industry has to climb to get this right.
But in other ways…it’s exciting.
Our industry has prodded the slowly waking giant, and it is clear that businesses, facilities managers, building managers and the amazing people who work across fire safety are making inroads into resolving fire door issues. There is a growing sense of shared-passion as we start seeing the humble fire door treated as any other hard-working asset in a building - with proper, frequent planned inspections and (dare I say it) maintenance.
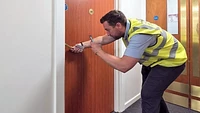
I’m going to put this out there; inspecting a door does not improve life safety in a building, providing maintenance to ongoing defects does.
It is important to know:
- How defects are resolved and what certification will be provided
- How specific works are programmed and implemented
- What Quality Assurance (QA) checks are completed to validate the quality of works
- Where the certification and data relating to the works is going to be held in years to come
So, although fire door inspections are a key part of building fire safety, focus surely has to move from inspection to maintenance regimes. Far too often, the Pre-Planned Maintenance (PPM) term is being used for fire doors, when actually no maintenance takes place, just inspection. This is often compounded with no clear budgeted plan for resolution, just another list of defects to consider.
Obligations under the Regulatory Reform (Fire Safety) Order (RRO) for frequent maintenance of fire doors is not fulfilled through regular inspection - this has to be combined with fixing the actual issues. Inspections completed every six to twelve months just to be inspected again when no works have taken place since original inspection, does not satisfy the RRO, does not contribute to building safety and is a waste of budget that could be directed towards resolution.
Erm…isn’t this article about inspection, not maintenance?
Yes, let’s get back on track!
Having said all this, the fire door inspection is the starting point. Whether dictated to a client through an expert Fire Risk Assessment (FRA) or considered as a programme across an estate of properties, the quality of the inspection is the leading factor in how likely the doors in a building are going to be made safer (note, I did not say compliant, safer is absolutely a step forward in some circumstances).
Competency and accreditation of fire door inspectors
It all starts with the person recording the data.
Are they competent? Do they have clear, demonstrable experience in inspecting fire doors? There are a range of ways in which you can demonstrate competence ie SKEB, (Skills Knowledge, Experience, Behaviour). Look for companies with third-party accreditation - such as LPS 1197, BM Trada or FIRAS - who are also ASFP members. Do they have set agreed protocols for carrying out inspections and have the processes in places to ensure fire door inspectors maintain the standards set by the third-party certification body?
The fire industry likes a good certificate. Here’s a top tip: make sure the certificate your inspector has does not have that small print, stating “this does not qualify this person to inspect a fire door”.
A fire door awareness course is a very useful thing; it helps building managers understand what to look for in a fire door, and what the common faults are - and start to understand what can be remediated and not. It gives valuable CPD points but may not mean the person can inspect to an appropriate standard.
Recording of fire door information
The fire door inspector should be recording the data electronically, noting defects and photographing/evidencing where the door specifically fails at each and every element. For instance, it is not unusual to see a single door with more than 5 images.
The first action of any surveyor should be to establish the original manufacturer and any certification of the door set. Whilst the door may present characteristics in keeping with a fire door, the most reliable way to establish its intended use is by locating the certification label and/or plug. Manufacturers labels can differ, however, the most commonly used format is shown below, and provides the fire performance, manufacturers contact details and certification.
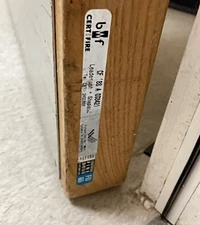
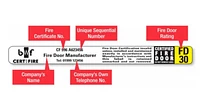
In some instances, even when a label isn’t present, a plug identifying the level of certification may be found if the original manufacturer operated under the BM Trada Q-Mark Certification Scheme.
Labels and/or plugs are typically found on the top of the hanging edge of the door leaf.
In addition, the inspector should be able to record clearly whether the defect is:
- A replacement part
- An adjustment or repair
- Something that is missing
- Damaged beyond repair
Ideally the door should be QR coded and linked to a plan of the building so there is no “on-site” confusion as to which door is which when potentially reviewing the inspection from a desktop.
The devil is definitely in the detail!
So, you now have a report. It has covered all the areas expected - the leaf condition, leaf gaps, frame condition, ironmongery and closers, vision panels, air transfer grills and signage.
This sounds detailed enough, right?
Well, sure, the categories are important, but now it is time to understand what detail is being recorded. If the right data is not recorded, it will be almost impossible to give an accurate assessment of costs to a contractor for remediation or replacement.
For a client, this means the contractor will either cost ‘in risk’ in the final assessments, and return a comparatively expensive quotation, or worse still, assume the lowest level of remediation for each category, returning a low-cost assessment. The latter will inevitably mean the hard-earned budget will not be met by the incoming contractor and variations against the original survey will be sought.
Common challenges and what to look for in a good fire door inspection:
A comprehensive door inspection should follow set agreed inspection protocols. As a business, we have sight of a wide range of inspection reports displaying various levels of detail. Some of the common challenges are:
- Leaf gaps – typically the recording of gaps in 7 locations for single door sets and 12 locations for double door sets. Simply noting that the door requires easing and adjusting is not enough. There could be a host of tasks required to make sure the door is finally remediated within tolerances - some requiring little time, others requiring full overhaul of leaf and frame. A contractor needs to know the gaps in several locations on the door set to be able to fully appraise and provide cost surety to the client
- Seals – if a door is recorded where requiring seals is the only remediation necessary, it is quite unlikely to be accurate. Depending on the required compliant seals, a contractor would need to know if leaf gaps are likely to require adjusting to fit the seals (see point above)
- Door type – it is important to note if the door is an FD30/FD60, a double, single, or leaf and a half. Understanding if the door requires a smoke seal is also important, especially when considering the threshold requirements
- Door and frame finish – ‘veneer, laminate, flush, painted’… Is the frame hard wood or soft wood? Often a door can be veneer, but the frame is painted – these elements make big differences to the final contractor assessment, and if this data is omitted from reports, it is likely contractors will seek variations at a later date
- Determining what can be repaired – while this is sometimes obvious, a good contractor will always suggest consultation with the manufacturer, or will undertake this on your behalf for commonly recorded damage, to understand what can and can’t be repaired. This is often something that needs closer attention at the point of completion, and the contractor may require more information to make an assessment
- Floor levels – often difficult to assess during survey, however, a common cause of threshold gap issues is not the door, but the floor level. Whilst there are often ways to resolve these issues, it is good to record concerns within the inspection itself
- Original ironmongery – for example, an understanding of whether the locks were originally supplied with the door, or as a tested solution with the door leaf blank. Any area of concern should be identified and may need further investigation
- Does it need to be a fire door? If it is not on a fire line in the fire strategy, it may not need to be replaced with a fire door, or vice versa. A fire door sign is not the leading indicator here
- And finally, it’s not always what is there that can be defective, it is what isn’t - for instance, a door may never have been fitted with a closer but may need one to be compliant. A door may not have a kick plate, but it may be highly recommended based on its location
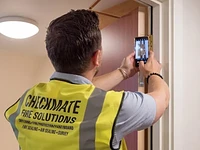
What can be hidden from view?
A visual inspection of a fire door, combined with manufacturer test evidence, gives a good assessment of how a door will perform against its rating in a real fire. However, ensuring a door has been fitted correctly in the first place can be hard to ascertain...
A fire door inspection may not identify if fire stopping behind the frame is present or compliant. It is always recommended that an architrave is removed on several doors to check this element. On larger schemes, this should be done on a number of differing locations of doors across a selection of floors – such as riser, cross-corridor, and bedroom doors. Inconclusive findings may lead to further investigative works to determine the best course of action. Without this information, clients can find significant variations when works commence.
So, what do you actually need?
Oddly a question that may not be easy to answer… but buckle in, because I’m going to do my best!
It is unlikely you just need to know if you are compliant or not. It is rare that an inspection will result in overwhelmingly compliant results. So, it is likely at some point that you will need answers, solutions, and - dare I say - estimated costs to put things right (or at least demonstrate improvements in fire safety).
So, if all the above points are prevalent in the assessment of cost, surely it is important to know the cost of every nut, bolt and minute of time spent on the door by a contractor?
Well, not always.
Sure, a contractor can cost works to a clear schedule of rates, and this can be achieved, however, this can also lead to significant variations, especially if time has passed between original inspection and approval (up to 6 months is not unusual - a lot can happen to a fire door in this period of time). Or, if you have chosen to inspect with one contractor and award works with another, differences of opinion may form, again, leading to variations.
Another way is to simplify, simplify, simplify! Let me break it down for you…
A contractor can:
- Provide rates that factor in a variety of defects within set bandings of remediation, this leads to significantly less variation on expected budgets
- Offer a fully fixed cost per leaf – potentially without the need for the cost of the survey in the first place
- Take a holistic approach and fix all defects, irrespective of whether they were recorded, allowing a provisional sum for expected levels of replacements
This method gives absolute cost surety and transfers risk to the contractor.
While there is no absolute method, understanding the client end point is important before committing significant sums on inspections - and often surety of cost runs alongside quality in this respect.
Prioritisation
Ultimately, it is up to the fire strategy of your building to determine what door is likely to be prioritised in front of another. There is a view that the most important fire door is the one immediately in front of where the fire starts. This said, a fire door inspection can at least look at the location of a fire door, and start the prioritisation process. A fire door that leads to a storeroom with no sources of ignition could potentially be considered as a lower risk than a plant room door, adjacent to the means of escape. The fire door inspection can consider these elements and provide clients with a pragmatic starting point to consider alongside their fire strategy.
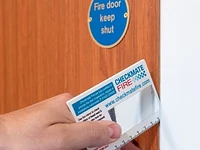
How long does a fire door inspection take?
Well, how long is a piece of string?!
There are many factors to consider – type of building, numbers of doors in each building, distance between doors, common area doors vs residents’ front entrance doors, who is making the appointments, what is the process for no access… you get my drift.
All these elements affect the amount of time spent inspecting a door. The maths is pretty straight forward though, as is this age old idiom…if you receive a range of quotes, cheapest is not always best.
Consider how long it takes to get proper detailed information recorded, the cost of getting the right trained individual and the right detail in your final report.
How often should I inspect a fire door?
Attention is drawn to Article 17 of the Regulatory Reform (Fire Safety) Order 2005. This highlights the requirement for maintenance of fire safety provisions, and advises you to set up a regular planned preventative maintenance programme for the works completed. In relation to fire doors, the following guidance could be adopted as defined in BS 8214: 2016, Clause 13, or in accordance with BS 9999: 2017, Annex I.
An example would be SFG20 23-17, as one of the adopted standards – largely by building managers and the FM industry - for the periodic maintenance of fire doors, which provides the guidance that there are 7 maintenance events that should be carried out. Tasks 1-5 should be at a monthly frequency, and undertaken by the facilities manager, task 6 is a 3-month check, again by the facilities manager, and task 7 is a six-monthly check which should be undertaken by a competent person.
In our opinion this approach is sensible, as a lot can change with a fire door between the 6 monthly competent checks and it is probably unrealistic to expect competent specialists to undertake checks at any greater frequency.
Do I need a fire strategy AND digital plans of my building?
Not really, but we recommend that every building should have a fire strategy that details policies and clear safe, escape routes.
I know…not necessarily the helpful answer you were looking for, was it!?
In terms of assessing fire doors, there is a risk that without either a fire strategy or digital plans, the inspection report may inspect doors that do not necessarily need to be fire doors.
Without plans, it is likely that ALL doors will be inspected just in case – and without a fire strategy it cannot be absolutely determined if the rating of the fire door is satisfactory. Just because it currently is an FD30 rated door, does not mean it should be. You may end up with an inspection report with more questions than answers. Having a strategy helps, and without that, a digital plan certainly does, as it enables doors to be marked onto a plan, detailing location and recorded information.
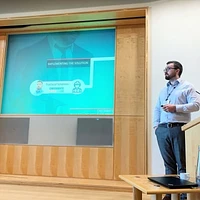
Next steps?
If you want to know more, or if you want a sneak peek at what a good inspection may look like, or maybe you just want to talk a bit more about your situation and what your options are, we are happy to have chat about how we can help.
We are only a phone call away. Alternatively, you can book onto our next seminar for some healthy discussion.
We can also help with getting the right fire-stopping/compartmentation survey should your fire risk assessment require it.
Please contact our Head of Technical, Damien Ward, on 07375508016 or damien.ward@checkmatefire.com for more information about how we can provide hassle free fire door inspections - or if you want to know how you can get a good digital plan and/or fire strategy should you need it to support any future inspection.
And if you made it to the end of this article, high 5 – I’m proud of you…we know it can be confusing!