The Importance of Passive Fire Protection in Buildings
It is hard to over-emphasize the importance of a passive fire protection (PFP) strategy and its subsequent governance in buildings. Comprising some kind of an assessment of the likely fire risks, an evacuation plan, and the means to deal with both, the absence of a robust strategy has long been a problem, only now properly appreciated.
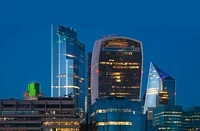
Regular inspections and maintenance by third-party accredited PFP firms, along with adequate information logging that audits any changes to the integrity of building compartments, offers a good opportunity to ensure a building remains fire compliant.
The primary concern of PFP is for life safety. Radiant heat is rarely the problem, although it can, of course, be fatal. Much more dangerous are the products of combustion (e.g. smoke). National and international regulations, codes and standards concentrate on these and related threats, many of which are well understood and for which there are good solutions. The formal penalties for getting PFP wrong include criminal conviction.
However, human health and safety is by no means the only objective of PFP. Other interested parties all have their own reasons for going beyond life safety. Building owners will also want to protect their property and the assets therein to avoid interrupting their operations. To attract purchasers and tenants, developers will need to be able to give assurances about fire protection. Insurers will also want to eliminate or mitigate all fire risks. Investors will demand best practice as a matter of due diligence. And building users will, depending on their fire risk exposure, want as much built-in fire protection as possible to save themselves the cost and delay of adding active systems and upgrades.
Fires are dangerous by their very nature, but they become catastrophic when they have the opportunity to spread from the room of origin. The point of PFP is to prevent this spread, or at least delay it. All too often, however, fires do spread, often because of faults with the construction of otherwise perfectly robust PFP design.
The finger of blame for these disasters is commonly pointed at the contractors who installed the measures incorrectly or the inspectors who approved them. However, the building owners also carry some responsibility if necessary inspections or remediation works are not carried out. While this once again highlights the importance of the PFP strategy, it also emphasises the need to specify that competent contractors, who are third-party accredited, are appointed to inspect and maintain passive fire measures.
This is especially true in new builds where primary designers leave the detail design to the main contractor. Since many aspects of PFP are hidden from view, retrospective fixes for poorly installed designs are disproportionately difficult and expensive. PFP in buildings affects almost every aspect of the design. The objective is to restrict the fire to a fire and smoke-resistant compartment long enough to allow people to escape safely and for the emergency services to attend.
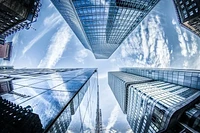
PFP should be proportionately balanced against active systems for an optimum cost-effective solution. The guiding principles are to:
- Communicate the PFP strategy to the whole project team;
- Consider the impact of design changes on the overall PFP strategy;
- Use fire-resistant building materials;
- Reduce the chances of fire spreading by secondary ignition;
- Design physical barriers to resist flame and insulate against heat;
- Design the structure to resist collapse or excessive deflection in the event of fire;
- Minimise the spread of smoke and other products of combustion in the event of fire
- Minimize the risk that fire can spread in from an adjoining building or other external fire source
- Facilitate access for fire-fighters
- Specify third-party certificated or otherwise quality assured fire protection products, service and service providers
These principles need to be applied to the following elements of the building, each a specialist field by itself:
- The structural frame: steel frames are particularly vulnerable. Steel loses strength quickly under quite low heat loads and so must be protected with board materials, or sprayed with intumescent paints or cementitious applications. Timber frames are combustible; they are usually protected by plasterboard. Concrete frames generally do not need protecting, although spalling can be a problem, particularly if it exposes steel reinforcement.
- The building envelope: as well as preventing fires from spreading internally, it is desirable to stop them spreading to neighbouring buildings and other assets too. There are many solutions, all of which of course must be thoughtfully designed.
- Doors and shutters: doors or shutters only need to be fire-rated if set in fire-rated walls, in which case their ratings must match in most circumstances. How they are intended to be used and by how many people will affect the choice of door-closer and other elements of door furniture. Correctly installed third-party certificated complete fire door sets are the preferred route to peace of mind.
- Compartment walls, floors and ceilings: compartment walls should run continuously to join the floor above to form an uninterrupted fire barrier, even through ceiling voids and roof spaces. Doors and glazing in them need equal fire-resistance in most circumstances. Any service holes through compartment walls should be kept as small as practicable and must be appropriately fire-stopped. The same is true for shafts running through floors or ceilings. And since these are hidden from view, contractual responsibilities for getting them right must be clearly stated.
- Firewalls or fire-separating elements – especially to preserve the means of escape: these are barriers that preserve escape routes and areas of especially high fire risk, such as cooking machines in food factories or fuel storage spaces. Doors, glazing and service penetrations need equal fire resistance in most circumstances.
- Floors generally: resistance depends on the material they are made from. Timber chars and is consumed at a predictable rate. Superheated concrete is prone to explosive spalling, which might expose steel reinforcement. Steel deforms and weakens catastrophically when exposed to heat. Proprietary fire protection products must be selected with care to suit the particular on-site conditions.
- Cavities: ceiling or wall cavities are protected from flames and smoke with barriers. Because they are hidden from view in the finished building, they must be designed and installed correctly, making it particularly important to clarify responsibilities in the contractual arrangements.
- Air distribution systems and ductwork: often left in the hands of a specialist sub-contractor, fire protection in the air distribution system needs careful attention. Methods include installing fire dampers where it passes through the compartment wall or floor, using fire-resisting ducts or enclosing the systems in fire-resisting shafts.
- Service ducts and shafts: ducts and shafts containing fuel lines and other building services can obviously help to spread fire and smoke and must be adequately fire-stopped wherever they penetrate compartments and other fire barriers.
- Pipe, cable and other services: where these penetrate fire barriers, they must be appropriately fire-stopped. The exact method will depend on what is penetrating the barrier and how the barrier is fire-rated. Large penetrations have the added problem of potentially weakening the structure, and so any seals will have to be capable of reinstating the structural integrity of the fabric as well as stopping any fire.
- Glazing systems: glazing in fire barriers such as compartment walls or ceilings must match their fire-rating. There are many products that maintain their integrity. Specifiers are increasingly selecting glazing that insulates against radiant heat as well, which is important along escape routes. Note that their frame and method of fixing is critical.